May 22, 2017
The vision of the DIMECC SIMP program (2014-2017) was to bring benefits from digitalization to the metals and metals production industry. The program focused on the digitalization of highly complex process chains by modeling, simulations, and analysis, which, in the end, will enable real-time predictive control in the plant environment. The advances made in the program have a clear impact on production and resource efficiency for one of the biggest export sectors in Finland. The final report presents the research results and impact of the DIMECC SIMP program.
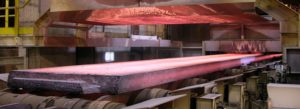
AvestaPolarit Stainless Oy
Resource efficiency is high on the EU political agenda. Digitalization of processes, process chains, systems and especially linking them in a mathematically and process control systemic and coherent basis is arguably a key component in realizing sustainability through resource efficiency.
To this end, the main aim of the DIMECC SIMP program was to further improve the already low environmental footprint of the Finnish Metals and metal products and to further increase its global competitiveness by integrating Digitalization and Sustainability in a system integrated manner. The DIMECC SIMP program had the objective to deliver system integrated sustainable metal production predictive control systems for three key Finnish industry sectors: copper, steel and stainless steel. The focus in the program was specifically on digitalizing complex process models and making them operable in real-time in a gate-to-gate systemic plant environment.
As world class players involved in the project. Altogether, 20 leading Finnish companies and 7 research organizations, came together to address sustainability in quantified manner. In addition, around 9% of the resources in SIMP have been dedicated to research with international partners. During SIMP, the program collaborated with more than 49 international research institutes and companies.
As a result, new and innovative models and measurement technologies have been developed in the program to optimize the production processes. The aim, throughout the program, has been to integrate these innovative models and measurement technologies as far as possible into the control systems of the production processes. Only by this system integration can the full benefit of the models and measurement technologies (the tools) be achieved. In the best cases, the tools have already been piloted in full-scale production tests, leading to significant improvements in economic, environmental, and social terms. In the years to come, we will realize the full benefit of this system integration, when even more tools originating in SIMP are developed for production use.
Take a closer look at the results of DIMECC SIMP program.